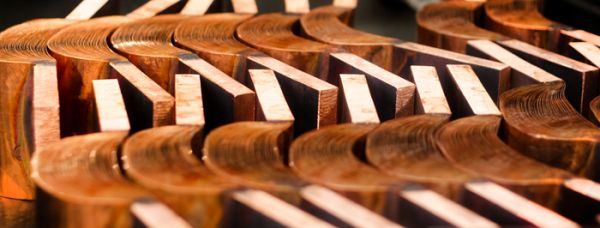
The Press Weld Process
Press welding is one of the most vital and active departments within the Watteredge manufacturing facility. This area handles a wide range of copper sizes and thicknesses and plays a key role in producing many of the company’s custom-engineered copper components. The press welding process requires a variety of different people and machines to produce the final product.
The process begins when operators deliver raw copper stock of the appropriate thickness and width to a designated shearing station. At this initial stage, precision is critical. The operator carefully measures and cuts the copper to exact lengths, verifying measurements of the copper throughout the shearing process to maintain quality and ensure consistency across all parts. This foundational step prevents downstream errors and upholds the high standards Watteredge is known for.
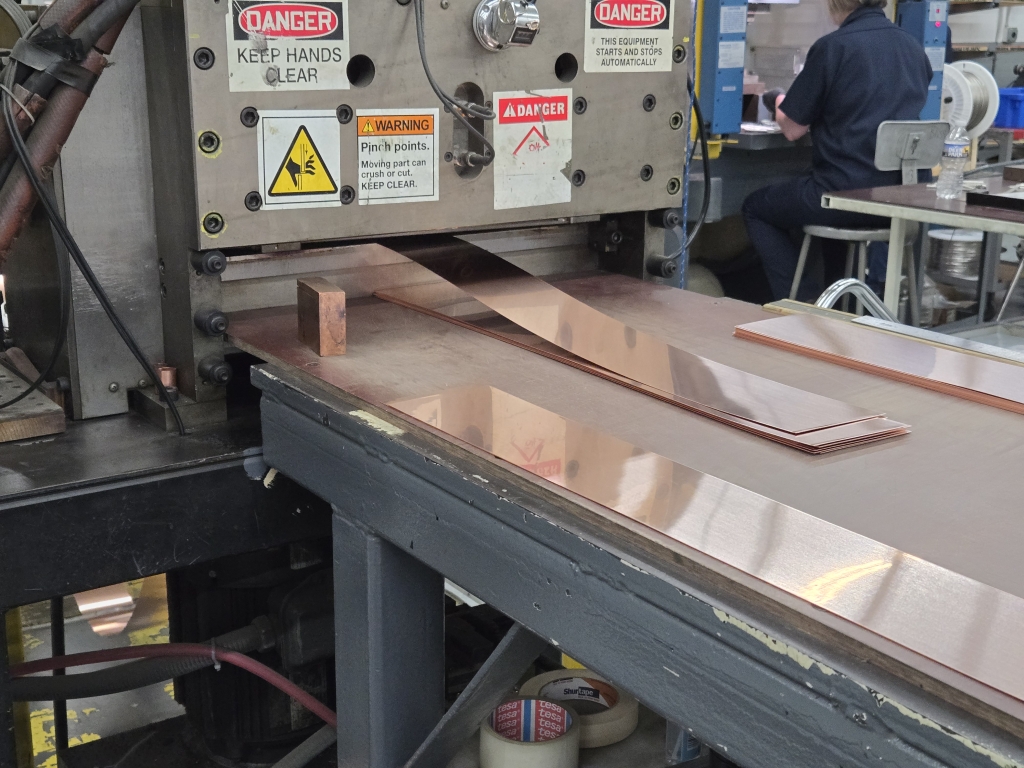
After cutting the copper strips to the required dimensions, workers tape them together to maintain alignment. This temporary bond keeps the pieces correctly positioned during welding. With the parts prepped, technicians move them to the press welding station for the next phase.
At the press welding station, skilled technicians apply high pressure and heat to fuse the copper pieces. This process creates a strong, unified structure and improves electrical conductivity. Typically, one section becomes rigid and solid, while others retain flexibility—depending on the component’s application. This balance of strength and pliability ensures optimal performance.
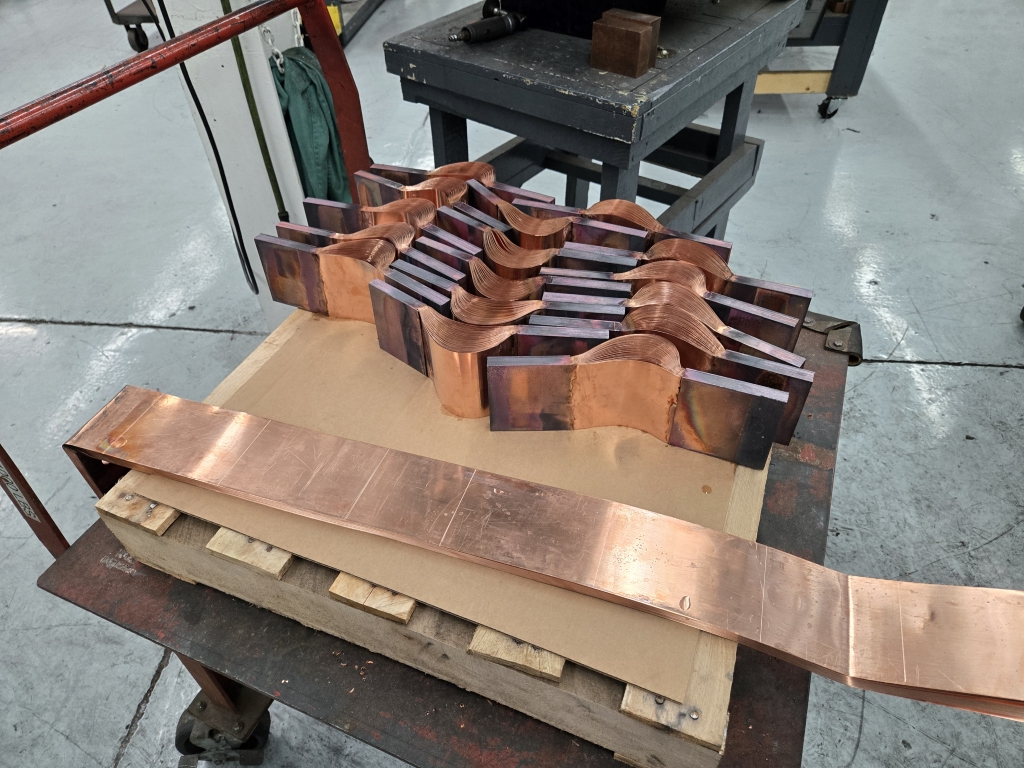
Post Press Welding
After welding, operators grind down the joints to remove sharp edges and surface imperfections. This step ensures both safety and functionality while preparing the part for any finishing treatments.
Depending on the part’s final use, the team may apply various finishes. These include electroplating with tin or silver to enhance conductivity and resist corrosion, or adding a nickel laminate, often used in flexible copper shunts. Workers may also apply protective insulation based on the product’s electrical or thermal requirements. Watteredge offers options like PVC, Teflon, and fiberglass, each selected for its performance benefits.
Once finished, the team either ships the component directly to the customer or incorporates it into a larger assembly. Many of these press-welded parts become essential components in copper shunts, braided flexible connectors, high-current switches, and other custom-fabricated copper products.
Subscribe to our blog posts so you can continue to get updates about future trade shows, job fairs, and information regarding Watteredge and its products and services!